Recuperación de calor para la cerámica italiana
Italia es famosa por su estilo y su calidad en la fabricación y diseño de azulejos utilizados en proyectos residenciales y comerciales alrededor de todo el mundo.
FECHA 2024-05-28Después de que un fabricante se dirigió a Alfa Laval con sus retos de recuperación de calor, un sistema utilizando un intercambiador de calor en espiral soldado resultó ser un éxito donde otros habían fracasado. El resultado fue un ahorro de 5 GWh de energía y 2500 toneladas de CO2 por planta y año, en un total de 9 plantas.
El reto planteado por el fabricante de baldosas se refería a una etapa crucial de su proceso de producción: el secado de las materias primas cerámicas. El fabricante utiliza un proceso de secado por pulverización, en el que una boquilla de alta presión pulveriza la mezcla cerámica húmeda en una corriente de aire caliente. Aquí el agua y los compuestos orgánicos volátiles se evaporan rápidamente de las diminutas gotas, dejando partículas cerámicas secas que se recogen para su posterior procesamiento.
Para reducir las enormes necesidades energéticas del proceso de secado, el cliente quería conseguir un precalentamiento de la mezcla antes del secado por pulverización. En intentos anteriores de recuperación y reutilización de calor habían fracasado, principalmente debido a las propiedades de la mezcla cerámica.
Además de ser muy abrasiva, la mezcla no es newtoniana, con un comportamiento irregular como el endurecimiento bajo presión repentina. Esto había provocado una rápida obstrucción y un rendimiento inestable en los intercambiadores de calor.
Pruebas para el éxito
Para cumplir los requisitos de resistencia, estabilidad y eficacia rendimiento, el equipo de Alfa Laval realizó una serie de pruebas de laboratorio con la mezcla cerámica. Tras discutir sus conclusiones con el cliente, se instaló un piloto a escala real utilizando un intercambiador de calor en espiral Alfa Laval en una de las plantas de producción.
El intercambiador de calor en espiral soldado de alta resistencia estaba colocado antes de la entrada al secador por pulverización. El calor residual de los motores de la planta se introducía en el intercambiador de calor para precalentar la mezcla cerámica. Este proceso permitió una reducción significativa de la carga del horno al corriente de aire calentado por gas, ya que se necesitaba menos calor para secar la mezcla ya precalentada.
El proyecto piloto fue todo un éxito, y el cliente instaló el sistema de precalentamiento de recuperación de calor en todas sus plantas de producción. Cada planta ahorra aproximadamente 5 GWh al año gracias a la reutilización del calor, con una reducción de las emisiones anuales de 2500 toneladas de emisiones anuales de CO2.
Ahorro de energía
5 GWh de energía
Reducción de emisiones
2500 toneladas de CO2 por planta y año
Ahorro de costes
220.000 EUR
Descarga el caso de éxito
Tecnología destacada
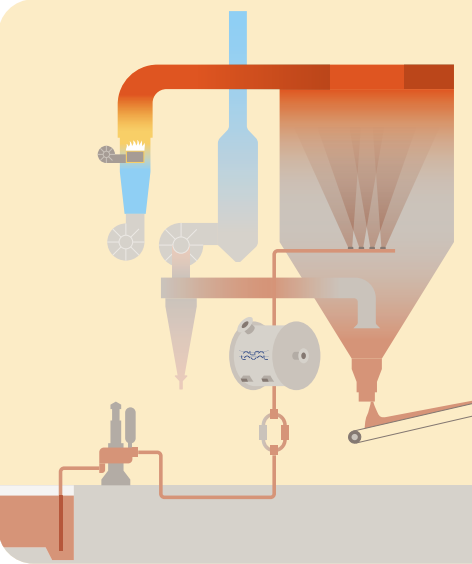
Etiquetas
Todo