Pasta perfecta: aumentar la capacidad de producción con Contherm Max
La creciente demanda de sus productos por parte de los consumidores puso de manifiesto un cuello de botella en el proceso de producción de Surgital, un destacado fabricante italiano de alimentos. Se necesitaba una solución innovadora para ampliar la capacidad y optimizar el rendimiento. El intercambiador de calor Contherm Max de Alfa Laval fue la respuesta, y su inclusión en el proceso de producción ha generado un aumento de la capacidad del 20%, además de recortar 36.000 € de la factura de electricidad y reducir las emisiones anuales de CO2 en hasta 150 toneladas en la planta de la empresa en el noreste de Italia.
FECHA 2024-03-11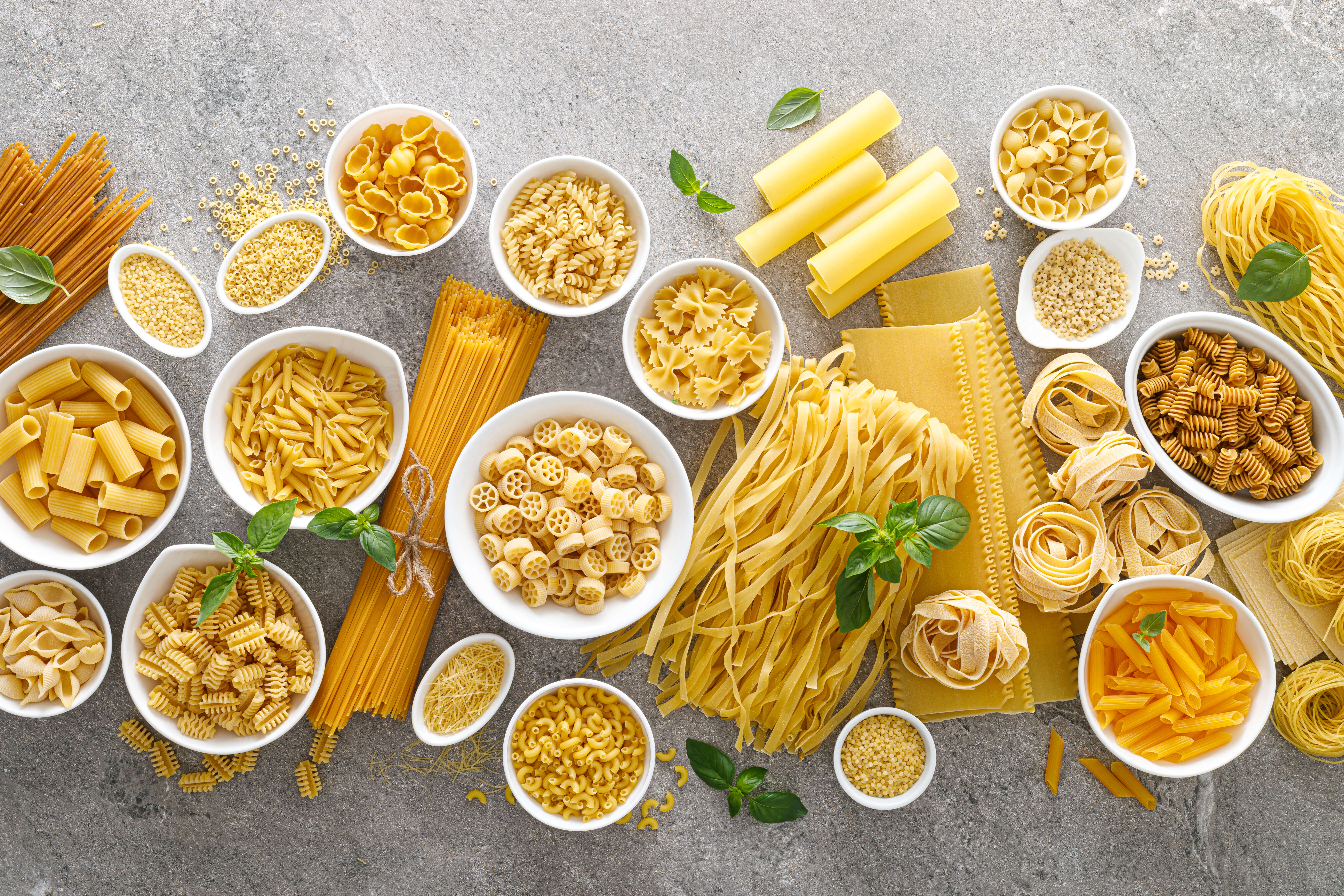
Surgital es el primer productor italiano de platos preparados ultracongelados, pasta y salsas. Fundada por la familia Bacchini en 1980, la empresa produce actualmente 175 toneladas de pasta fresca, 90.000 platos preparados en porciones individuales y 30 toneladas de salsas para pasta al día en su centro de producción de la provincia de Rávena.
La popularidad y el aumento de la demanda de estas salsas para pasta, producidas en forma de cubos congelados, pusieron de manifiesto un bloqueo que limitaba la capacidad en el proceso de enfriamiento. En última instancia, esto llevó a Surgital a recurrir a la experiencia combinada en procesos y equipos de Tetra Pak y Alfa Laval para ampliar la capacidad de producción de la planta y aumentar el rendimiento del producto.
El equipo del proyecto necesitaba resolver un problema relacionado con el tiempo necesario para enfriar suficientemente la salsa para facilitar el proceso de corte de los cubitos.
El proceso original constaba de varias fases, empezando por intercambiadores de calor tubulares, que enfriaban la salsa desde la temperatura de cocción hasta 45°C. A continuación, se realizaban otras dos fases de enfriamiento en túneles consecutivos de enfriamiento forzado por aire. La primera de ellas reducía la temperatura del producto a -2°C para poder cortar la salsa en cubos, y la segunda bajaba la temperatura a -18°C, lista para el envasado y la expedición.
El problema radicaba en el tiempo que el producto debía permanecer en el primer túnel de enfriamiento para alcanzar los -2°C, lo que repercutía negativamente tanto en el proceso de cocción anterior como en el de congelación posterior.
La solución que Alfa Laval y Tetra Pak idearon fue un paso de enfriamiento adicional: la instalación de un intercambiador de calor de superficie rascada Contherm Max para enfriar la salsa de 45°C a 15°C. Este descenso de la temperatura permitió aumentar el rendimiento en el primer túnel de enfriamiento y eliminó el cuello de botella.
"La instalación del Contherm Max ha permitido a Surgital alcanzar el objetivo de ampliación de capacidad y rendimiento", afirma Edoardo Bacchini, de Surgital.
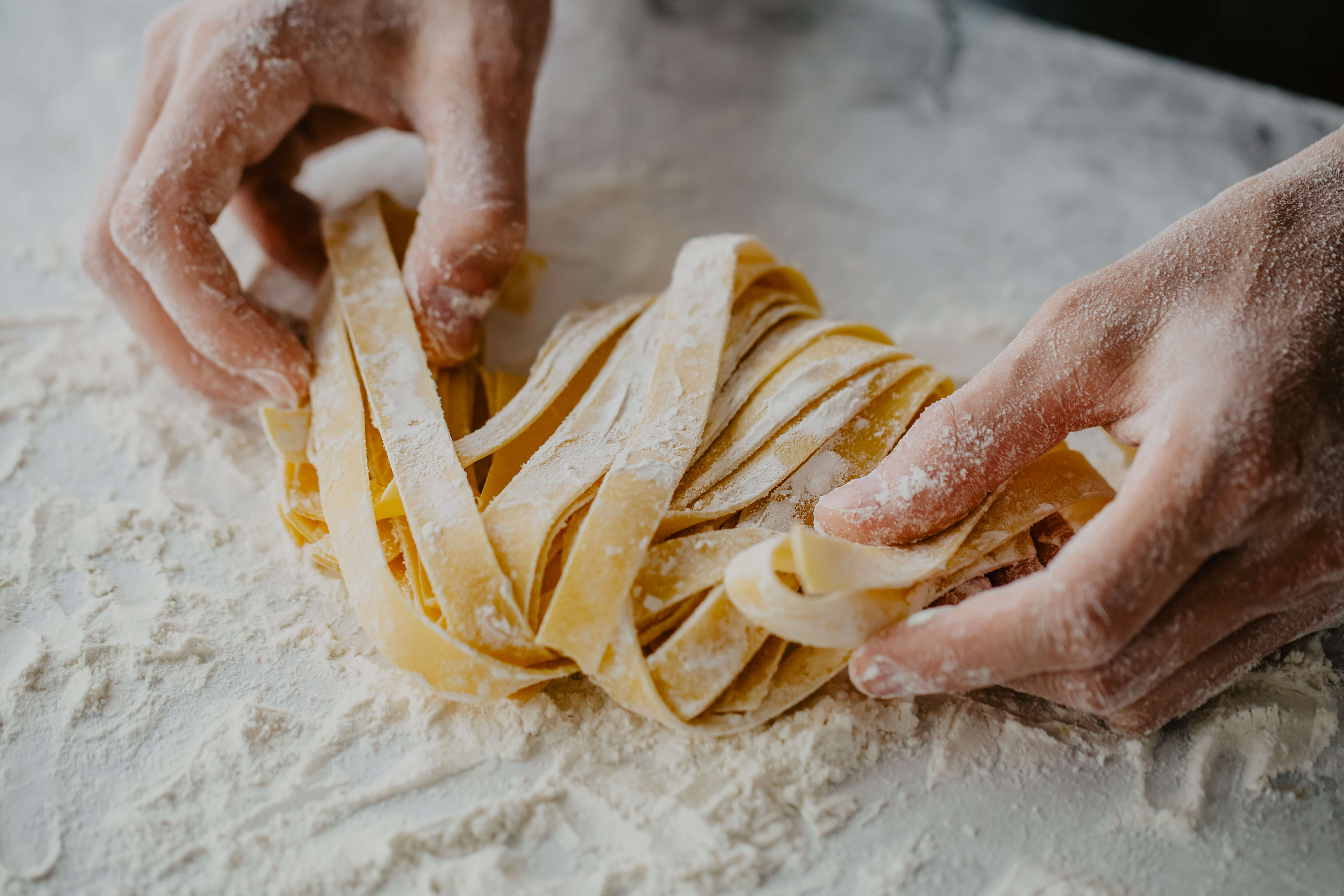
"La solución propuesta fue significativamente más rentable que las otras opciones", dice Simone Incerti de Tetra Pak Italia. "El preenfriamiento consistente entregado por el Contherm Max ha mejorado la calidad del producto, permitiendo la producción de cubos de salsa de un peso más uniforme y una forma más consistente entre diferentes lotes."
La introducción de un intercambiador de calor de superficie rascada en la línea para realizar un preenfriamiento eficaz del producto permitió a Surgital utilizar uno de los sistemas de refrigeración existentes para obtener el aumento de capacidad deseado, explica Giovanni Treglia de Alfa Laval.
"De lo contrario, para obtener un aumento de capacidad comparable, habría sido necesario ampliar el túnel de enfriamiento de 1er paso forzado por aire, lo que habría requerido duplicar el sistema de refrigeración actual y habría consumido hasta 200 MWh más de electricidad al año", continúa. "Gracias al nuevo Contherm Max, el túnel de enfriamiento del primer paso proporciona una temperatura del producto 3 K más fría que antes, lo que supone un ahorro adicional de hasta 10 MWh de energía eléctrica en el túnel de congelación posterior (segundo paso de enfriamiento). En total, la solución implantada está ahorrando 36.000 euros en energía eléctrica, lo que equivale al consumo anual de electricidad de 30 hogares, y reduciendo las emisiones de CO2 en hasta 150 toneladas al año".
Tecnologías destacadas
Tiempo de actividad
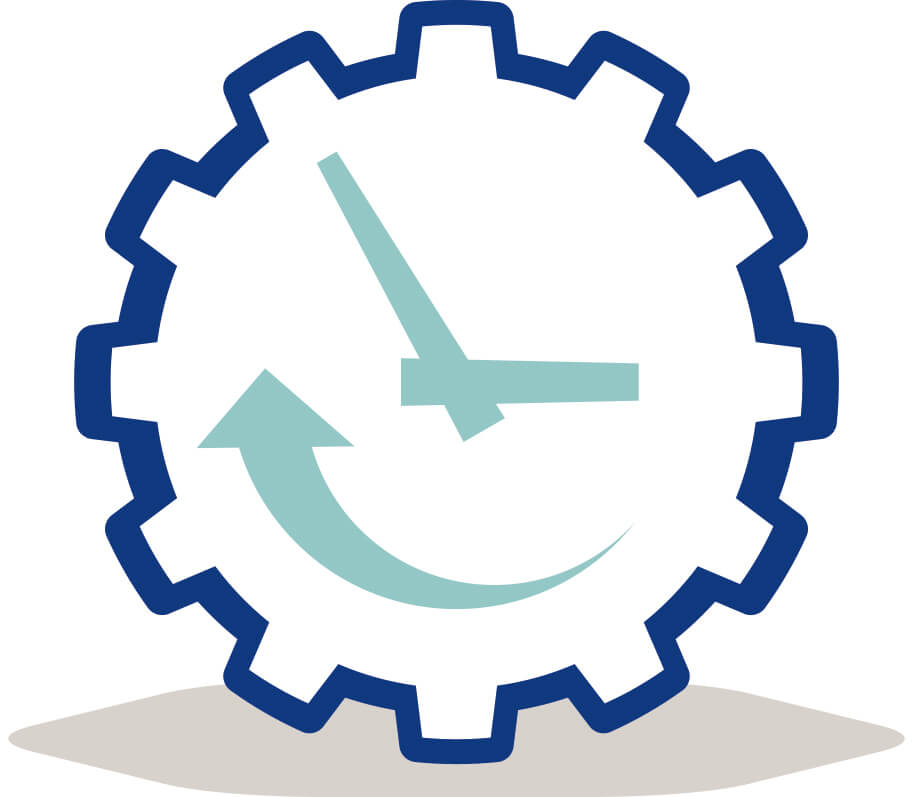
20% de aumento de capacidad
Reducción de emisiones
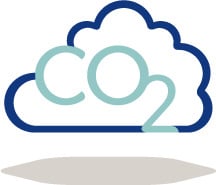
Reducción de las emisiones de CO2 en hasta 150 toneladas al año
Ahorro de costes
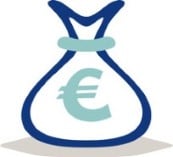
Reducción de 32.000 euros en los costes anuales de mantenimiento
Ahorro de energía
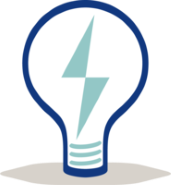
36.000 euros de ahorro de energía eléctrica
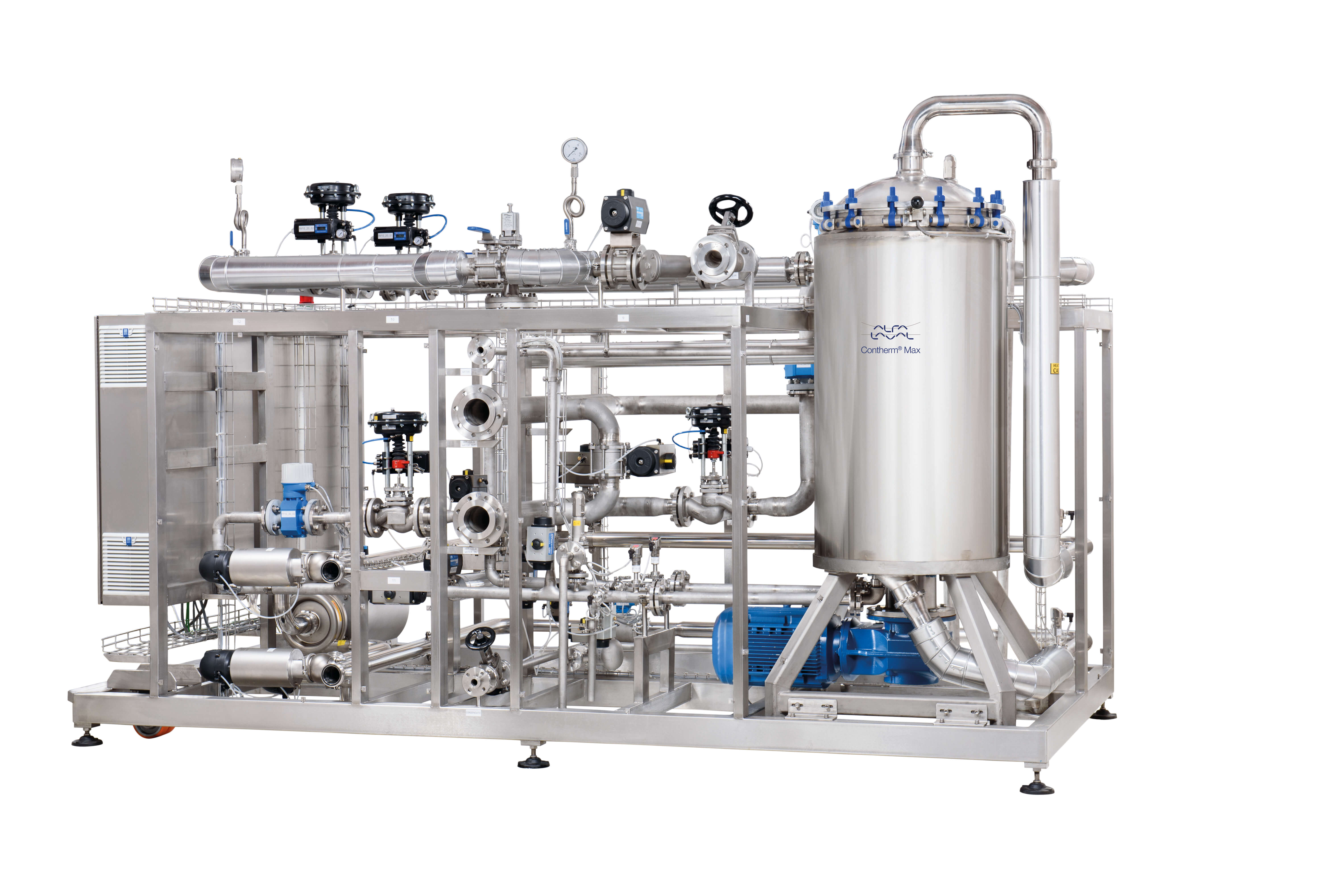
Las ventajas de esta solución eran:
- Un 20% más de capacidad
- Tratamiento de enfriamiento uniforme y temperatura del producto mucho más fría al inicio del primer túnel de enfriamiento.
- Menor temperatura del producto a la salida del túnel, que alcanza los -5°C y permite un corte más preciso de los cubos.
- Tiempo reducido en el primer túnel de enfriamiento forzado por aire que permite una microcristalización más profunda del producto y una mayor calidad.
- Una reducción de 32.000 euros en los costes anuales de mantenimiento gracias a la inclusión de una bomba de doble tornillo.