La competencia en los procesos aumenta la flexibilidad y la productividad en la mezcla de jarabes para bebidas.
¿Quiere estar al día de las últimas tendencias en bebidas sin perder relevancia ni rentabilidad? La innovación constante es imprescindible para los fabricantes de bebidas. Para satisfacer los gustos cambiantes de los consumidores, un fabricante mundial de refrescos se enfrentaba a una mayor demanda de una gama más amplia de productos con una mayor variedad de ingredientes. Gracias al amplio conocimiento de Alfa Laval sobre el diseño de salas de jarabes para bebidas y sus innovadoras soluciones de mezcla, la empresa pronto podrá disfrutar de una mayor flexibilidad en los procesos y de una producción por lotes un 50 % más rápida.
FECHA 2025-05-19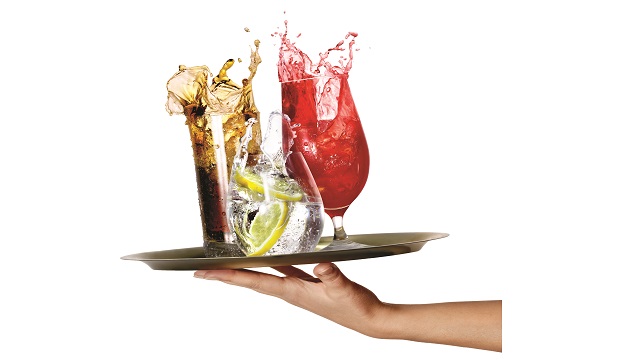
Process competence and proof-of-concept trials wins customer trust
Processing liquid and dry ingredients into complex beverage syrup formulations requires production flexibility and speed. Alfa Laval demonstrated a deep understanding of the challenges faced by the global beverage manufacturer, winning the trust of key decision-makers at its central R&D and engineering departments. Trials convinced the manufacturer that changing the existing syrup room process design with innovative mixing solutions from Alfa Laval would enhance process flexibility and productivity and add customer value.
50% faster batch production time
Alfa Laval’s process knowledge and commitment to enhancing productivity cut syrup processing time from two hours to one hour per batch. Replacing existing syrup room mixing technologies with the Alfa Laval Hybrid Powder Mixer in combination with the Alfa Laval Rotary Jet Mixer provides additional hours of production time each day. The faster rate of syrup production also cuts energy costs.
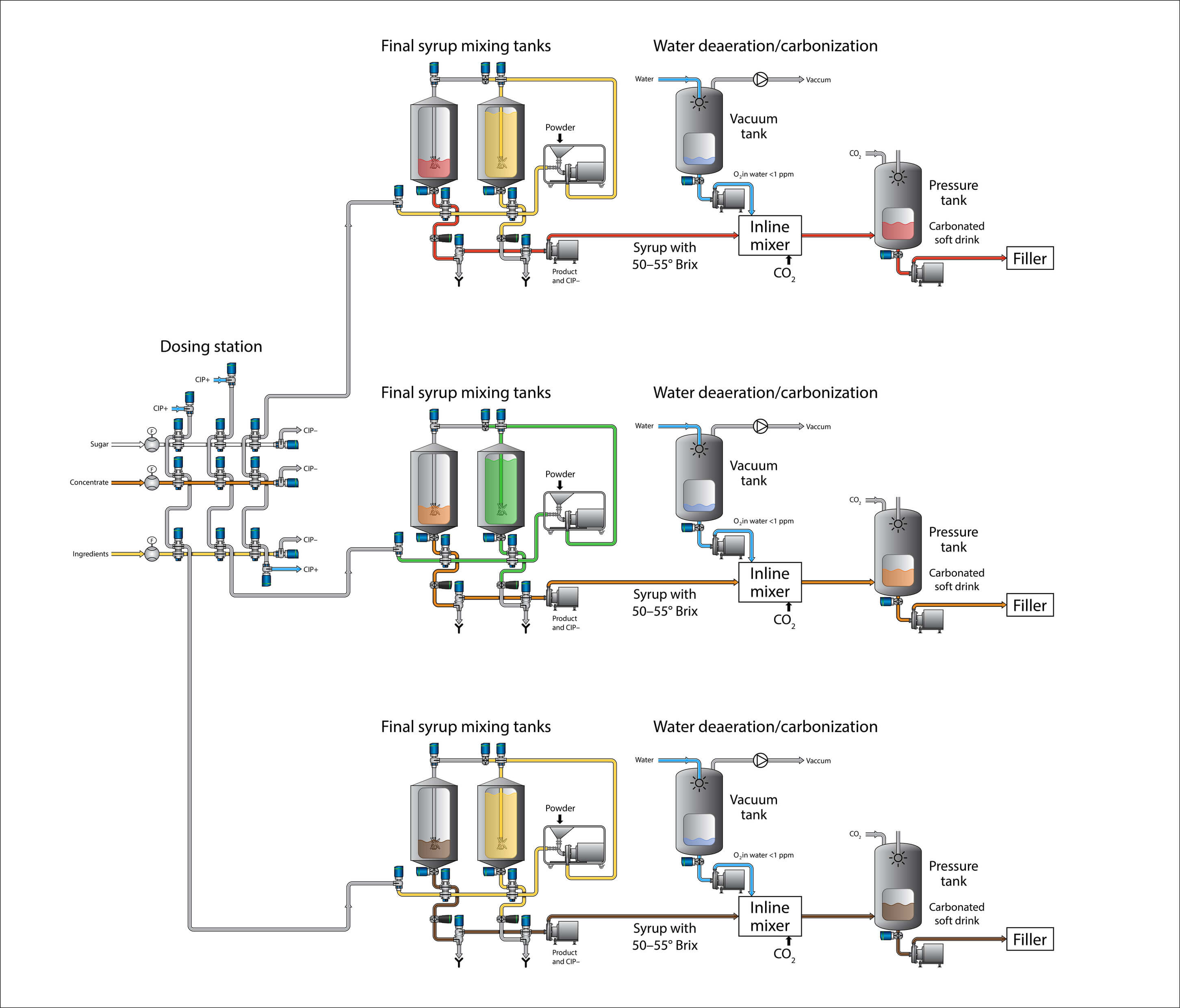
Less time for maintenance
Reducing maintenance time is another example of Alfa Laval process ingenuity at work. Maintenance for the Rotary Jet Mixer requires a single service engineer working at floor level for one to two hours; in contrast, the existing large agitator requires several service engineers working an entire day on a multilevel service platform. Less downtime translates into more production uptime.
Increased worker safety
The same is true of liquid-powder mixing. Ingredient handling and dosing with the Alfa Laval Hybrid Powder Mixer occurs at floor level, resulting in easier handling and increased worker safety. This eliminates the need for workers to carry 25-kilogram bags to the upper-level platform and pour ingredients into the tank through the access port.
Streamlining production with mixing innovation
The unique design of the Alfa Laval Hybrid Powder Mixer together with the Rotary Jet Mixer outperforms the previous setup in the beverage syrup room, takes up less floor space and requires less investment in building service platforms. Alfa Laval teamed up and worked tirelessly with system integrators to design a mixing solution that produces more batches of complex syrup formulations – safely, quickly and efficiently.
Sustainable optimization
The next step? The company asked Alfa Laval to with its global sustainability manager to reduce emissions and introduce greater energy and water efficiency throughout the plant. A testament to Alfa Laval’s process competence and ability to optimize processes and, add value and lift competitive advantage.